oil & gas
Typical Material Grade Used but not Limited to:
C95400
C95500
C86300
C93200
C93800
Bronze parts play a significant role in the oil and gas industry, where reliability, durability, and resistance to harsh conditions are essential. The industry involves the extraction, transportation, and refining of oil and gas, often under extreme conditions such as high pressure, high temperatures, exposure to corrosive substances, and abrasive materials. Bronze, with its unique combination of properties, makes it an ideal material for many critical components in this sector. Here’s a detailed look at how bronze parts contribute to the oil and gas industry:
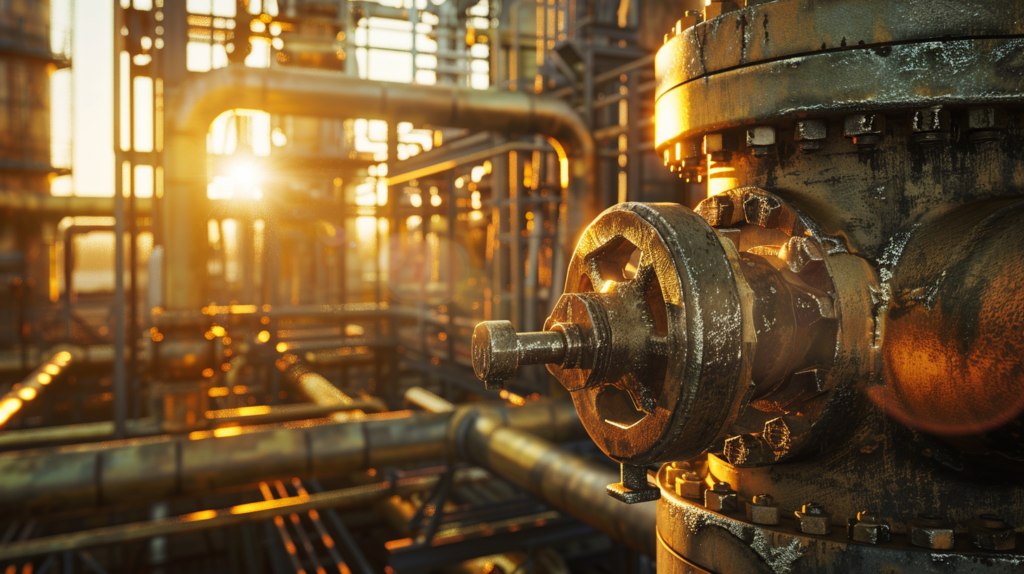
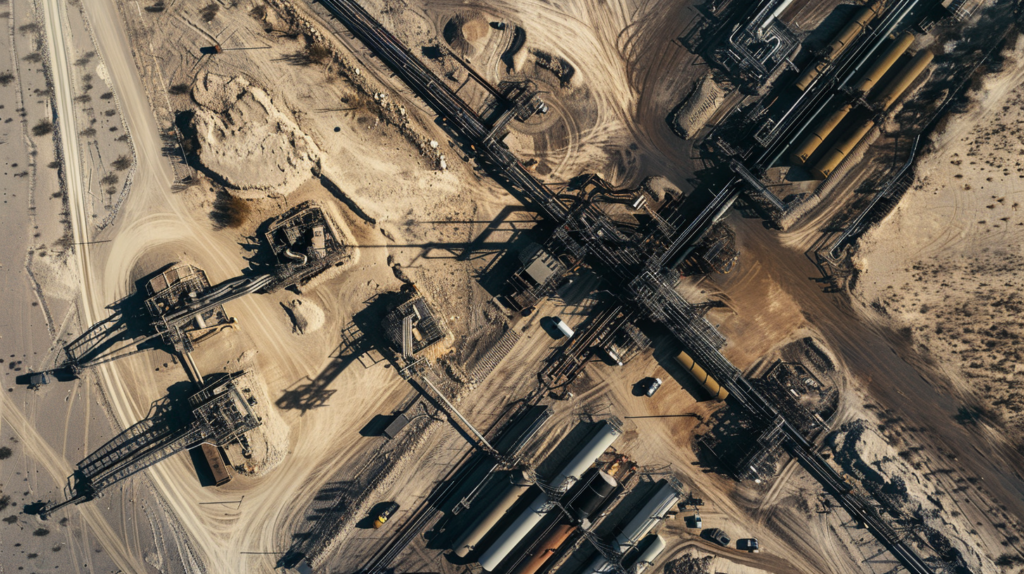
- Corrosion Resistance: In the oil and gas industry, valves are exposed to aggressive environments, including corrosive gases, acids, and chemicals. Bronze alloys, particularly those with a high copper content, offer excellent resistance to corrosion, ensuring that valves perform reliably over time without significant degradation from these harsh substances.
- Wear Resistance: Bronze’s ability to withstand wear from fluids and gases passing through valves makes it an ideal material for valve seats and valve stems. These parts are critical for maintaining control over fluid flow, pressure, and temperature in oil and gas systems.
- High Load and Friction Resistance: In the oil and gas industry, machinery such as pumps, compressors, and drilling equipment experience high friction and heavy loads. Bronze bearings and bushings are commonly used to reduce friction and wear between moving parts, helping to extend the lifespan of these machines.
- Self-Lubricating Properties: Bronze is known for its self-lubricating qualities, making it particularly useful in oil and gas equipment where maintaining lubrication can be challenging due to the environment. It helps to minimize friction, preventing overheating and premature failure of components.
- High-Pressure Sealing: Bronze is commonly used in seals and gaskets in oil and gas pipelines and equipment. These parts are crucial for preventing leaks of gases and liquids under high pressure. Bronze’s ability to maintain its integrity under extreme pressure and temperature makes it ideal for sealing systems, ensuring that systems remain secure and efficient.
- Chemical Resistance: In the oil and gas industry, equipment is often exposed to chemicals like natural gas, crude oil, and other corrosive substances. Bronze’s resistance to corrosion and chemical reactions ensures that seals and gaskets continue to perform effectively without degrading.
- Corrosion Resistance: Pumps are used extensively in the oil and gas industry for moving fluids, and they often handle corrosive materials. Bronze components in pumps, such as impellers, bearings, and shafts, help improve the pump’s longevity and performance by offering resistance to corrosion and abrasion.
- Strength and Durability: Bronze’s high tensile strength allows it to withstand the stresses associated with high-pressure pumps, providing reliable performance in both upstream and downstream applications.
- Components in Drilling Rigs: Drilling operations require heavy-duty machinery exposed to high pressures, harsh chemicals, and abrasive materials. Bronze components, such as bearings and bushings in drilling equipment, help ensure smooth operation and reduce wear, preventing the need for frequent replacements.
- Durability Under Extreme Conditions: Bronze’s resistance to wear and high temperatures makes it suitable for the tough conditions encountered in the drilling and extraction process, improving the efficiency and operational lifespan of the equipment.
- Corrosion and Pressure Resistance: In pipelines and offshore oil platforms, flanges and fittings are critical for joining different sections of pipes and components. Bronze is used in these applications because of its corrosion resistance and ability to withstand high-pressure conditions. It ensures that connections remain leak-free and secure under the extreme pressures found in subsea or onshore oil and gas facilities.
- Reliability in Harsh Environments: The oil and gas industry often operates in challenging environments such as offshore rigs or pipelines in corrosive or marine environments. Bronze’s resistance to saltwater corrosion makes it ideal for these applications.
- Thermal Conductivity: In oil and gas refineries, heat exchangers are used to transfer heat between fluids in processes such as distillation and refining. Bronze, with its excellent thermal conductivity, helps to efficiently transfer heat while resisting corrosion and scaling from fluids. This enhances the overall efficiency of the system and reduces the risk of malfunctions.
- Corrosion Resistance: As heat exchangers often deal with aggressive chemicals and corrosive fluids, bronze’s resistance to corrosion ensures long-lasting performance, reducing the need for frequent maintenance or replacement of heat exchange components.
- Conductivity and Durability: Many oil and gas operations use instrumentation and electrical components to monitor and control equipment. Bronze, especially copper-based alloys, is used for electrical connectors, terminals, and other components due to its excellent electrical conductivity and ability to resist corrosion, ensuring reliable electrical connections in rugged environments.
- Safety and Efficiency: Electrical components in hazardous areas, such as offshore platforms or oil refineries, must remain safe and functional even under harsh conditions. Bronze’s properties help prevent failure due to environmental exposure, enhancing safety and operational efficiency.
- Marine Environment Durability: Offshore oil and gas operations require equipment that can withstand the corrosive effects of saltwater. Bronze is highly resistant to saltwater corrosion, making it an ideal material for subsea and offshore oil rigs where components are submerged in saltwater for long periods. This includes parts like flanges, fasteners, and valve seats.
- Strength in Extreme Conditions: The high-strength, corrosion-resistant properties of bronze are crucial for equipment exposed to high pressures and fluctuating temperatures found underwater, ensuring equipment remains operational in these extreme conditions.
- Valves and Pump Components: In oil extraction processes, valves, pumps, and regulators must perform reliably under varying pressures and temperatures. Bronze’s strength, resistance to corrosion, and low friction properties make it suitable for these applications, ensuring smooth and efficient operation even in harsh field conditions.
- Durability and Low Maintenance: The reduced need for maintenance due to the long lifespan of bronze components in field equipment helps oil companies minimize downtime and avoid expensive repairs in remote locations.
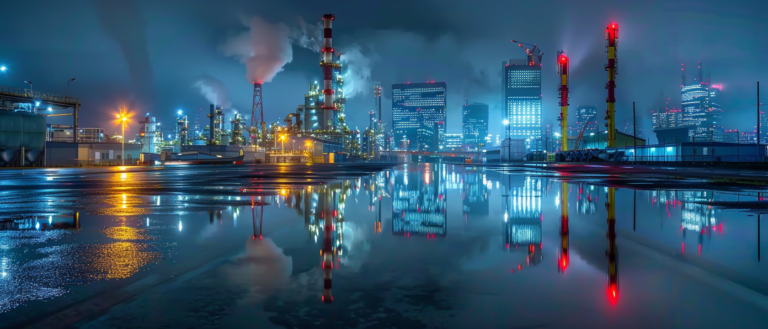
Bronze parts play a critical role in the oil and gas industry by providing wear resistance, corrosion resistance, high strength, and thermal and electrical conductivity across a wide range of equipment. These include valves, pumps, bearings, seals, gaskets, drilling equipment, and subsea components. The ability of bronze to withstand the challenging conditions of high pressures, corrosive environments, and abrasive substances makes it an indispensable material in ensuring the reliability, efficiency, and longevity of oil and gas operations, from upstream extraction to downstream refining.